Preparation and cutting performance of TiCN-based functionally gradient cermet
Titanium carbonitride (TiCN)-based cermet is a new tool material developed by adding TiN on the basis of the TiC-based cermet.
Due to its high hardness, high thermal stability, excellent creep resistance, and wear resistance, TiCN-based cermets have successfully replaced WC-based cemented carbides in the field of semi-finishing and finishing.
Homogeneous TiCN-based cermets are prepared by powder metallurgy with TiCN as the main hard phase, Co and Ni as the binder phase, and adding other carbides and nitrides.
With the development of cutting, especially the development of high-speed cutting, the environment of cutting tools is more complex, which puts forward higher requirements on the wear resistance of cutting tools.
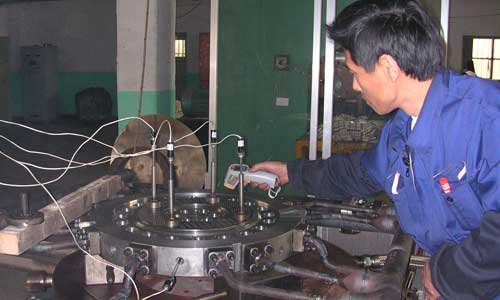

In the mid-1990s, Japanese scholar T.Nomura and others adopted in-situ diffusion technology to prepare gradient structure alloy with N-rich surface, which greatly improved the wear resistance and fracture toughness of cutting tools.
Later, Austrian scholar W.Lengauer et al. have systematically studied the phase formation, metallurgical reaction, liquid phase formation temperature, degassing temperature, and microstructure of functional gradient hard materials prepared by in-situ diffusion, zhang armed et al. studied the influence of TiCN content on WC-based cemented carbide gradient coating.
A large number of research results show that W-rich tough layers can be formed on the surface of tool materials through vacuum sintering, laying a foundation for the preparation of high-performance coatings, through controlled atmosphere sintering, Ti-rich cubic carbide and nitride layers can be formed on the surface of the tool, and its cutting performance is better than homogeneous cermet and coated hard alloy.
However, with TiCN as the main hard phase, there is little research on the preparation of gradient cermet.